As a manufacturer of sustainable and renewable wood products, we set ourselves apart by building strong distribution partnerships and ensuring that products are delivered on-spec and on-time.
Wood is Good
Wood is the ultimate natural, renewable and versatile building material. From houses and infrastructure to musical instruments and books, wood products not only support our basic need for shelter, but they also enrich our lives and standard of living. When wood products are manufactured in a way that is environmentally sustainable and socially responsible, we can all feel good about the significant role they play in our lives. Some reasons to feel good about wood products:
- Trees use solar energy and carbon dioxide from the atmosphere to grow;
- Wood products store carbon for the lifetime of the product;
- Wood has incredible cellular strength making it strong and stable while also pliable;
- When compared to concrete or steel building materials, wood products require less energy and water to manufacture, have superior insulation properties, and mitigate climate change due to emitting fewer greenhouse gases in manufacturing (see research from the Consortium for Research on Renewable Industrial Materials);
- Sustainable forest management contributes to climate resilience, including reducing the risk of wildfire and accelerating reforestation and carbon sequestration following disturbance;
- Humans are intuitively drawn to visible wood surfaces, and studies have shown that we have a positive physiological response to visible wood. A study by the University of British Columbia and FPInnovations found the presence of visual wood surfaces in a room lowered sympathetic nervous system activation—the system responsible for physiological stress responses in humans (FPInnovations 2011);
- The wood products industry provides meaningful economic and social benefits in our communities and beyond;
- Wood is versatile, and anyone can work with it using basic tools and skills.
Market Opportunities
We’ve outlined above how experts advocate the use of wood from sustainably managed forests as a preferred building material to mitigate climate change (SRCCL, Chapter 4). We promote these and other environmental benefits of building with wood through the Softwood Lumber Board. We are also actively supporting the Georgia Forestry Association, which has championed the establishment of a state carbon registry intended to encourage mass timber construction as a sustainable development solution in Georgia.
Another expanding market opportunity is the production of biofuels from lumber manufacturing and bush residuals. Throughout our operations we have been forming relationships with renewable energy producers and facilitating an efficient supply chain. We currently use and sell sawmill residuals for renewable energy, and the demand for these low-emission energy sources is growing with the transition to a low-carbon economy. We are also exploring opportunities to increase the use of bush residuals for energy production while balancing this with retention of beneficial residuals that provide habitat, support biodiversity or mitigate erosion. In our US South region, we have had success chipping and selling a portion of the logging debris from stumpage tracts for use as biomass fuel. For more information on how we use mill residuals, see Optimizing Material Use on the Environmental Management page of our website.
Responsible Resource Use
At Interfor, we recognize the responsibility we have when working with valuable forest resources. We maintain and maximize the value of every tree harvested through sustainable forest management, sawmill optimization, investments in technology, and a culture of operational excellence. We embrace innovation and we support our operations so they can be nimble, seeking the best use for every species and grade in our geographically diverse operations.
We work with distribution partners, secondary manufacturers, and other members of our industry to provide a range of products for a variety of end users. This entails partnerships, built on trust and honesty, that allow us to explore value creation collaboratively. The result is driving value and ensuring cost-effective products are available for end users ranging from professional and custom builders to homeowners and hobbyists.
Adding Value with Mass Timber & Engineered Wood Products
Engineered wood products are produced by binding wood fiber with adhesives, creating products that retain many of the desirable characteristics of wood with enhanced strength and durability. Mass timber, a relatively new engineered wood product, uses layers of lumber and adhesives to create large and exceptionally strong structural components such as posts, beams and panels. Mass timber is engineered to be used in structural load-bearing applications and is an environmentally friendly substitute for carbon intensive materials such as steel and concrete.
At our Sault Ste. Marie plant, Interfor produces I-joists, a strong, lightweight engineered wood structural product designed for use in residential and commercial floor and roof construction. This facility combines flange stock from internal lumber production and oriented strand board web stock to produce a wood structure that functions similar to an I-beam with enhanced structural properties. I-joists are used extensively in residential floor and roof framing. We also supply secondary manufacturing partners with the wood fiber required to produce engineered wood components, and work with them to identify economically viable options to maximize the use of our forest resources.
By embracing the highest standards and advancing innovation in our manufacturing operations and woodlands, we keep our workplaces safe, increase efficiency, improve environmental performance, and deliver high-quality products.
Investing in Modern, Efficient Technology in Our Mills
For the last 10 years, we’ve spent an average of more than $148 million each year upgrading or investing in our existing facilities and systems and employing the latest technology.
We are seven years into a multi-year strategic capital investment program, designed to increase production capacity, improve lumber recovery and enhance our product mix. While the program has focused predominantly on our facilities in the US Southeast, it includes projects in our US Northwest and BC Interior Regions. Over the next several years, we will be focusing on various investments that are expected to grow lumber production, further optimize conversion costs, improve lumber recovery, and enhance grade and product mix. This will help position our portfolio of manufacturing operations as some of the most competitive in the industry and ensure their safe, high-quality, efficient and sustainable operation through all market cycles.
Strategic Projects Completed or Active (2019-2024)
- Major rebuild, Monticello 2019
- Major planer upgrades, Eatonton 2020
- Major planer upgrades, Georgetown 2020
- Primary breakdown upgrades, Georgetown 2020
- New kiln, Perry 2020
- New kiln, Adams Lake 2021
- Auto-grader and planer upgrades, Baxley 2021
- Kiln conversion, Bay Springs 2022 – 2023
- Major sawmill upgrades, Eatonton 2023
- New planer upgrades, Castlegar 2023
- Sawmill upgrades, Perry 2023
- New kiln, Grand Forks 2023
- Kiln conversion, Bathurst 2023
- New planer, Thomaston 2024
Investing in Modern, Efficient Technology in Our Woodlands
We invest in new technology to be used in the woodlands we manage, and we support investments made by the timber harvesting companies and landowners who work with us. Some highlights include:
- Equipping all staff with satellite communication devices to support safety while working in remote locations;
- Assisting wildfire fighting efforts by using drone-based infrared imagery in collaboration with the BC Wildfire Service to detect hot spots outside of established wildfire guards;
- Using handheld thermal cameras in logging operations to improve early detection of possible fire starts;
- Acquiring highly detailed remote sensing LiDAR (Light Detection and Ranging) data to inform inventory, planning and development across our operations;
- Employing spatial operational planning modeling to support sustainable harvest plans;
- Surveying and tracking forest operations and inventories using drones;
- Using GPS (Global Positioning System) technology as well as fixed and dashboard cameras at our sites in trucks and mobile equipment to improve and promote high safety standards; and
- Utilizing a GIS (Geographic Information System) to collect, manage and report on roads, operations and safety.
Creative and Advanced Use of Technology to Manage Forests
In our Canadian woodlands, we use drones and GIS to collect information and track work needing to be done. For example, we survey the final locations of built roads using drones, and we complete road inspections on GPS-enabled handheld devices. In both cases, the use of technology facilitates efficient data entry into our mapping and information systems. The map points can also be provided digitally to our contractors along with work prescriptions, so they know exactly what needs to be done and where.
In the Pacific Northwest, we completed a thermal camera trial in 2023 that streamlined fire watch operations. In 2024, our woodlands team rolled out thermal cameras to all our contract harvest and road building operations in the region. The agencies we work with in the region, including the Oregon Department of Forestry, Washington Department of Natural Resources, and the U.S. Forest Service, support the project, which exceeds timber contract and fire safety requirements.
Investing in Research
Research in partnership with other organizations plays an important role in ensuring the efficiency and effectiveness of our operations and forest management activities.
In northeastern Ontario, our woodlands operations are participating in a research study investigating the use of mycorrhizal fungi to inoculate tree seedlings as an alternative to herbicide application. The project is led by Indigenous-owned Wahkohtowin Development GP Inc. and Mikro-Tek. Interfor contributed 1,030,400 seedlings and provided data, records, and in-kind expertise from our forestry team. In 2024, 50% of the jack pine seedlings planted by Interfor in the Pineland and Spanish Forests were inoculated with mycorrhizal, and plans are in place to inoculate 100% of the jack pine and black spruce that will be planted in these forests in 2025.
Our Ontario woodlands team carried out a trial in 2024 on the Pineland Forest in northeastern Ontario to evaluate the effectiveness of using a motorized brush saw as an alternative to herbicide tending for the removal of competing vegetation in existing plantations.
In 2024, our BC woodlands completed a Steep Slope Tethered Harvesting Study in our Grand Forks and Castlegar operations. They developed best management practices for this relatively new harvesting technology to reduce the risk of undesirable soil disturbance or landslides, and will continue to refine it through ongoing monitoring.
In BC, our woodlands operations have partnered with the University of British Columbia (UBC) Faculty of Forestry to support research projects to improve identification of marbled murrelet habitats and to develop predictive ecosystem mapping for the entire province. We have also:
- Supported a hydrological modeling project by Selkirk College in southeastern British Columbia focused on accurate assessment of hydrological impacts of forest development and climate change in snowmelt watersheds;
- Installed and retrieved trail cameras to support the BC Wildlife Federation’s work studying and helping to restore mule deer populations; and
- Provided a field site for sampling to support a UBC graduate student’s research project focused on analyzing greenhouse gas emissions from heartwood rot.
Interfor is also a member of the National Council for Air and Stream Improvement (NCASI), a research organization that conducts basic applied scientific research to support the forest industry in achieving environmental and sustainability goals.
Commitment to Customers
We understand that our customers make plans and decisions that rely on us delivering our products on time. That’s why we consider our forecasted shipment week as a promise. Every order is managed through our forecast shipping alignment process and tracked at each step along the way. On-time shipments are a key metric for our team, and we track and report on this weekly.
We are committed to promptly responding to and addressing any concerns or issues that arise regarding our products. When a customer complaint is received, a sales representative starts a resolution process, which includes written responses and requires a documented resolution for an issue to be deemed closed. We also have a process that helps us identify potential issues and make changes proactively to avoid them. We deliver unmatched customer care by tracking every complaint as a metric and reporting on it, and, as a result, complaints are rare relative to the number of orders we take.
Customer Safety
Our commitment to safety includes an assurance to customers that our products will meet their needs and industry grade standards. Our mills have quality control programs in place to ensure that products meet exacting grade standards approved by the American Lumber Standard Committee (ALSC) Board of Review in the US and the Canadian Lumber Standards Accreditation Board (CLSAB) in Canada. Our products are regularly inspected by third-party grade inspection agencies to ensure our grading is accurate. Auto-graders, a significant and valuable investment, are favored in our operations as they provide safer and more accurate grading and result in a more consistent product offering to our customers. Today, all Interfor mills use auto-graders.
We provide information to help ensure our customers and employees handle and use our products safely. Information on health risks related to working with our products is available on our website and in our Safety Data Sheets.
In the last 3 years, Interfor has not had any of the following:
- Violations or non-conformance with regulatory labeling and/or marketing codes;
- Legal fines/settlements for false, deceptive, or unfair marketing, labeling, and advertising.
- Product recalls; or
- Legal fines/settlements for violations or bribery, corruption or anti-competitive standards.
Green Logistics
We look for opportunities to maximize efficiency and minimize environmental impacts associated with our supply chain and logistics. Examples of this include:
- Optimizing configurations of log packages for water transportation to ensure both efficient and safe delivery;
- Maximizing cubic volume or weight limitation of each shipment to ensure the greatest efficiency of available logistics capacity;
- Utilizing technology to ensure overall freight distance is minimized in meeting customer obligations and on-time performance;
- Aligning transportation mode preference to maximize economic efficiencies, with rail being favored for most medium- and long-haul destinations in North America;
- Increasing rail utilization for medium- and long-haul lumber shipments from our mills in the US South; and
- Using a transportation management system that enables us to access and leverage truck transportation capacity and support better utilization of dedicated fleets.
We use metrics to track our performance on these initiatives and use targets to drive improvement.
Fleet Efficiency
We reduce our fossil fuel consumption and improve emissions by continuing to phase out older, less efficient vehicles.
In 2024, we rolled out a company-wide idle reduction initiative for mobile heavy equipment at our sawmills. We collected baseline data on idle time and showed sawmill employees the benefits of reducing idle time. We ask that they shut off their vehicles when it is safe and the weather permits. With a mix of automatic shut-off technology and a change in operator prioritization, we aim to reduce idle time across all our divisions, saving fuel and decreasing GHG emissions.
Transition to a Low-Carbon Economy
The transition to a low-carbon economy is a significant opportunity for Interfor as we produce carbon-friendly products. A range of policy, legal, market and technological advances in energy production also supports our reduction of fossil fuel consumption. In addition to modernizing our operations, reducing energy consumption and lowering GHG emissions, we are taking steps to move toward a low-carbon economy and mitigate the associated risks. These include:
- Engaging with peers and customers to improve consistency in accounting and reporting on climate-related metrics;
- Using energy dashboards for each of our operations so we can regularly review GHG emissions and energy use;
- Continuously improving and reviewing our GHG inventory, including undergoing third-party limited assurance annually to validate our methodology and reporting; and
- Staying abreast of government strategies that apply to our operations and the public forest lands managed by Interfor, including:
- The BC government’s CleanBC Roadmap to 2030;
- The Ontario government’s Forest Sector Strategy, Forest Biomass Action Plan, and Environment Plan; and
- US climate directives and policies.
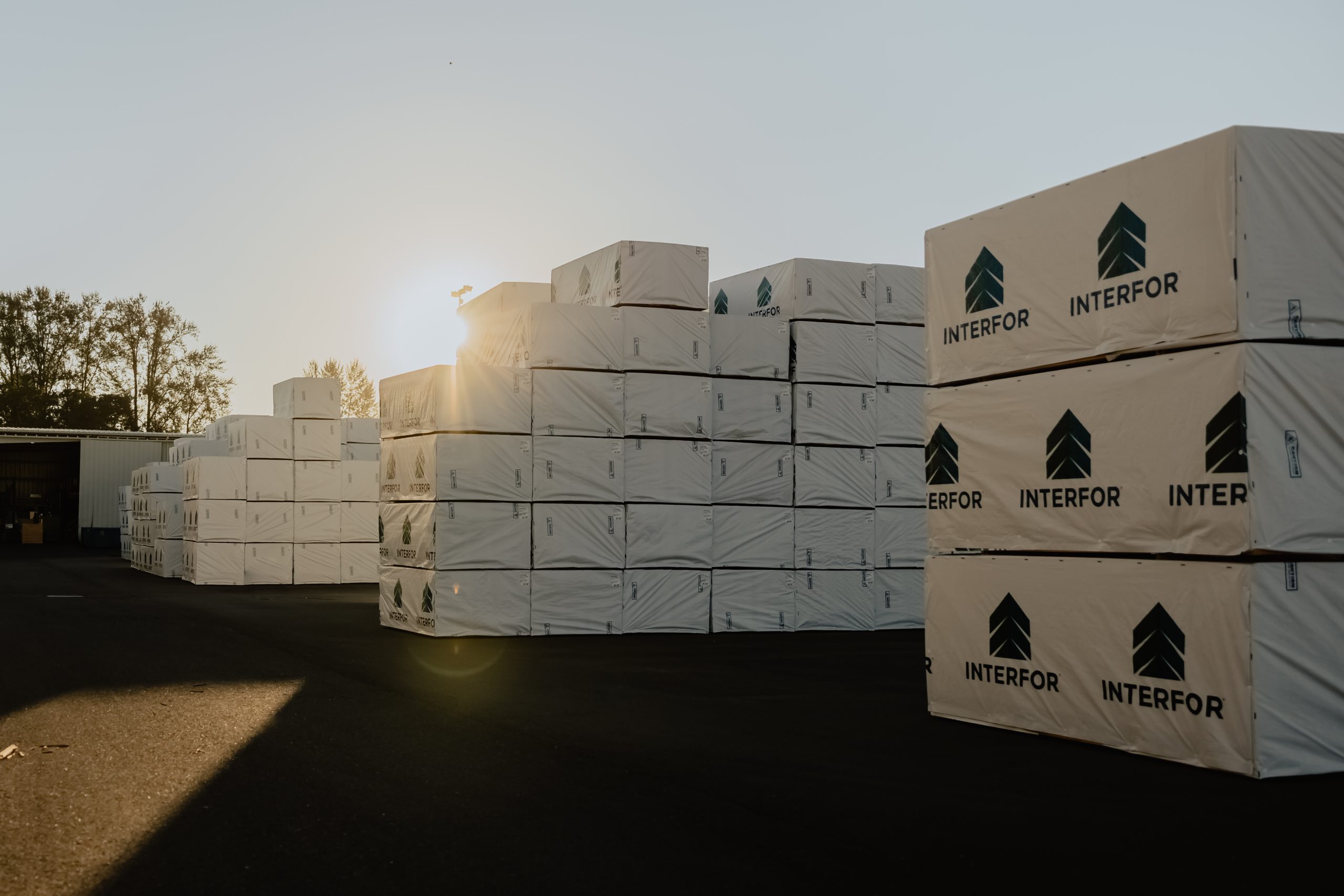
REFERENCES & METHODOLOGY
We are committed to transparency in our reported metrics and continuous improvement of our methodology. Download our References & Methodology document.
Sustainability
Building value through sound environmental, social, and governance practices
Our commitment to sustainable growth has been the foundation of our success, and to a broader extent, the success of our partners and the communities we serve.
Check out our Sustainability Report and explore how Interfor and our partners are creating a safer, more sustainable, and equitable future for all.