We maintain an internal Environmental Management System (EMS) that provides a structure to identify, address and manage environmental issues for all our manufacturing facilities and woodlands operations in the US and Canada:
Policy: Our EMS is guided by our Environment Policy.
Verification: Periodic audits—both internal and independent third-party — are conducted to verify our EMS effectiveness and compliance.
Training and awareness: EMS awareness is part of the onboarding for new staff and woodlands contractors. We also have annual refresher training, EMS field tours, and regularly report issues at business review meetings.
Internal and external communication on EMS issues: Our operations complete quarterly reports of environmental incidents that are provided to our executive team. When they are above certain thresholds they are reported to our Board’s Environment & Safety Committee. Indigenous communities and regulatory authorities receive reports of incidents as applicable to their respective territories and jurisdictions.
Auditing and Measuring Performance: In our manufacturing operations, we use environmental monitoring programs that cover aspects such as water quality, air quality, waste management, fuel handling, spill and fire prevention and preparedness. We conduct annual EMS audits. Monitoring and auditing for our forestry operations is covered under the Certifications section of the Sustainable Forestry page.
Environment Team
Originally formed in 2020, the Environment Team is made up of environmental experts from each of our manufacturing operating regions. Team members meet quarterly to share expertise so they can improve the consistency of our EMS implementation and environmental performance across our manufacturing facilities.
Some highlights from the Environment Team’s work in 2024 include reviewing and revising Interfor’s EMS Manufacturing manual, and the continued development of operational tools such as environmental manufacturing playbooks and training materials. These are being implemented across our manufacturing operations to reinforce our commitment to environmental compliance and promote best practices.
Air Emissions
We minimize air emissions from our manufacturing facilities using pollution control technologies suited to each site. We identify and report the air emissions produced as required by applicable legal and regulatory requirements.
Our sawmills use a variety of pollution control mechanisms to reduce particulate matter emissions, including cyclones, baghouses, and electrostatic precipitators (ESPs). ESPs are pollution control devices that use electrical energy to remove particulate matter in the exhaust system of boilers which are used to heat kilns. According to the EPA, ESP’s are capable of particulate collection efficiencies greater than 99%.
For additional details on our air emissions, please visit our Sustainability Report.
Spill Prevention and Response
Fuel and chemical handling, including storage, is a key part of our Environmental Management System. Our manufacturing facilities and woodlands operations have strict requirements that specifically address handling fuel, chemicals, regulated or hazardous waste, and dangerous goods. In addition to maintaining emergency spill response kits and/or secondary containment systems, we use spill plans and emergency spill response training to ensure our teams are well prepared in the event of an incident.
Each spill is reported to the applicable authorities in accordance with local regulations and is subject to internal investigation, clean-up, and corrective action plans.
Emergency spill response training is a key component of spill preparedness and response plans at many of our sites. This training helps our teams understand exactly what to do in the event of a spill and prepare them for the challenges they may encounter.
For additional details on our reportable spills, please visit our Sustainability Report.
We have key pilot projects across our mills that are helping us reduce water use and waste. As well as reinforcing our culture of environmental responsibility, this has a positive impact on the local environment. Here are some examples of our achievements, proving that sustainability is local.
Waste Reduction Projects
Our Preston Division set a target to recycle 75% of aluminum cans onsite. The effort is still in progress in partnership with the Georgia Sheriffs’ Association to raise funds for Georgia Sheriffs’ Youth Homes. Additionally, the site was able to reduce overall landfilled waste by 22% in 2024.
Our Nairn Centre and Timmins Divisions set targets to divert 100% of key recyclable items identified in their current waste streams from landfill. Together, the two mills diverted 11.6 tonnes of waste from landfill in 2024. Our Ear Falls, Elk Lake and Sault Ste. Marie Divisions completed recycling audits in 2024, and have set targets to recycle 83% of key recyclable items identified in their audits. This is expected to divert 8 tonnes of waste from landfill.
Our Adams Lake Division set a target to divert 700 tonnes of waste from landfill in 2024. It established a partnership with Spa Hills Compost to recycle wood ash, a residual produced from burning bark for biomass energy that has agricultural benefits including balancing soil pH and replenishing nutrients like calcium, magnesium and potassium. By the end of 2024, 1,280 tonnes of wood ash had been diverted from landfill and Spa Hills Compost had distributed it within the local farming community. The division also began recycling wooden pallets that can be upcycled into new products such as furniture and garden boxes. In 2024, we partnered with Valley Pallet Plus, a family-run pallet recycling business in Lumby, BC, to divert 150 pallets from landfill.
Byproducts, Waste & Recycling
We sell, recycle or repurpose more than 99% of our byproducts, which include sawdust, shavings, chips and bark. While historically many of these residuals were landfilled or incinerated without energy recovery or landfilled, today most are sold, recycled or repurposed for the production of green renewable energy, panels, medium-density fiberboard, pulp, paper, as well as used for landscaping and animal bedding. We also produce limited amounts of other hazardous and non-hazardous waste and recycling.
Recycling Programs
Our Burnaby, BC, Head Office is in a BOMA BEST Certified Gold building and partakes in a comprehensive recycling program including organics, batteries and e-waste. Our other offices and operations have recycling programs for materials from paper and cardboard to scrap metal and used oil.
Use of Recycled Materials
With the exception of two of our facilities, Interfor is a primary manufacturer. Our Cedarprime facility remanufactures lumber produced by our primary sawmilling operations, creating value-added products. Our Sault Ste. Marie facility produces engineered wood products known as I-joists which are used for floor and roof applications. They are produced using lumber flanges from sawmills combined with oriented strand board (OSB). The use of recycled wood or fiber is not applicable to our manufacturing processes.
Optimizing Material Use
We have sales programs in place to maximize the use of wood residuals which other companies turn into panels, medium-density fiberboard, pulp, paper and green renewable energy, including both wood pellets and biomass for power plants. A smaller portion of our residuals is used for mulch by soil and landscaping companies or for animal bedding. Interfor also uses residuals as a renewable heat and power source to dry lumber in our kilns.
In addition to residuals, another byproduct of lumber production is short trim ends from sawn lumber. Trim ends are used or sold for energy or remanufactured into trusses, pallets, finger-joint studs and parts for furniture and cabinets. We are exploring innovative tools with our contractors to minimize residuals left on harvesting sites. In BC, we are currently working with several of our pulp mill partners to increase our use of bush residuals by processing unused material from our harvesting operations into biomass fuel. In our US South region, we have chipped and sold residuals from harvesting operations on stumpage tracts for use as fuel. We seek to balance utilization with the retention of beneficial residuals that provide wildlife habitat, support biodiversity, and can be used to mitigate erosion. Residuals left in the bush also continue to store carbon for the short term, provide important habitat supporting biodiversity, and return nutrients back into the soil as they decompose.
For additional details on our waste and residuals, please visit our Sustainability Report.
In 2024, we completed installation of water meters at 100% of our sawmill facilities, helping detect anomalies in our water consumption and allowing us to pinpoint and fix leaks, leading to reduced water consumption. For additional details on our annual water withdrawal, please visit our Sustainability Report.
We also continued our efforts toward water reduction efforts through specific projects at our mill sites, including:
- Our Port Angeles Division saved more than 400 cubic meters of water in 2024 by continuing to operate waterless urinals, a pilot project initiated in 2023.
- Our Elk Lake Division uses a calcium mixture for dust control, which reduced the site’s water usage by 7,000 cubic meters in 2023 compared to past years. By continuing to use calcium for dust control in 2024, the site reduced water consumption by 95% from the past annual average.
Access to water is a universal human right. Interfor’s operations do not include any water-intensive processes, and none are within regions with high or extremely high baseline water stress according to the World Resources Institute (WRI) Aqueduct Water Risk Atlas.
As a small water user, our wastewater discharge is limited and the jurisdictions in which we operate employ a range of permits and authorizations with associated requirements to govern wastewater. In our industrial operations we use various methods to minimize impact on water quality and ensure compliance with site permits, including oil-water separators, settling ponds and bioswales. We conduct sampling as needed to meet permit requirements and inform management decisions on improving water quality, and we also use site maintenance practices such as sweeping, and erosion and sediment control measures.
Our manufacturing and forest operations Environmental Management System includes specific standards such as fuel and chemical handling and spill prevention measures to protect water, soil, and air quality. Our woodlands riparian management commitments define reserve and management zone buffers that are to be left around streams, wetlands and lakes in our harvesting operations to protect water quality, quantity, Indigenous values, and riparian habitats, as set out in applicable regulations.
Maintaining natural drainage patterns is a core element of our standard operating procedures, and our soil management objectives contribute to water quality by protecting soil structure and productivity as well as preventing soil erosion.
Our woodlands operations use stakeholder engagement and specific measures regarding community watersheds to mitigate potential impacts to drinking water. Although we do not have any water-intensive operations, we are committed to continuous improvement of our environmental performance.
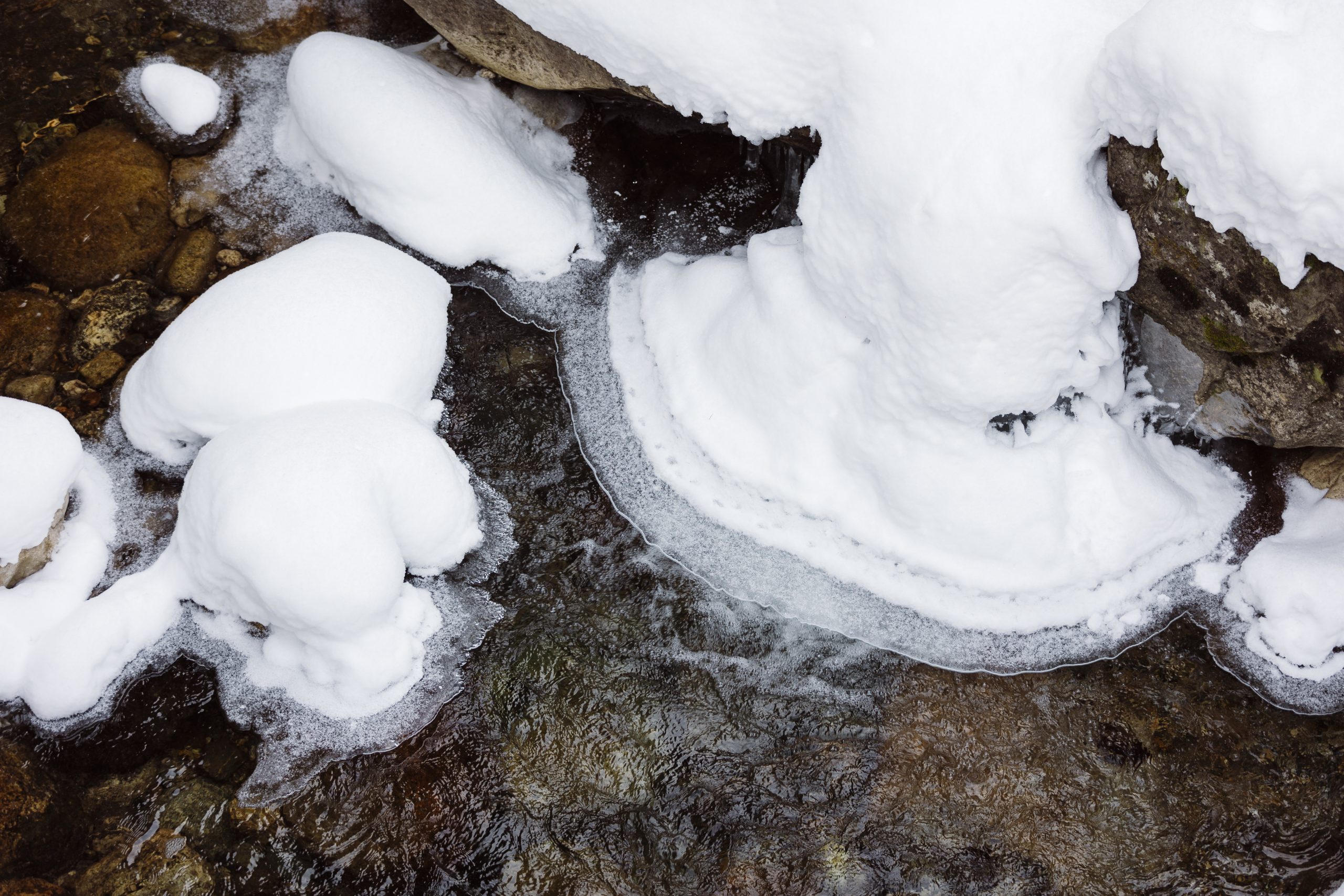
REFERENCES & METHODOLOGY
We are committed to transparency in our reported metrics and continuous improvement of our methodology. Download our References & Methodology document.